En inre, bärande kärna glidformsgjuts under hösten 2012. I mars 2013 lyftes en stor byggkran upp ovanpå taket på denna kärna, för att vidare fungera som bas för montaget av UBABs element. Bärande betonginnerväggar stabiliserade sedan med solida betongbjälklag, våning för våning, tills tornet var rest. Totalt 10 000 m² innervägg och 18 000 m² bjälklag från UBAB. Själva kärnan innehåller två trapphus. Ett riktigt spektakulärt inslag var när 60 våningar betongtrappor från UBAB lyftes från bil på marken, upp 100 meter i luften och firades ner genom kärnan till sin position.
Projektet enligt UBABs ”Ett hållbart byggsystem”:
1. Förprojektering
Under förprojektering och projekteringsstadiet hade man stor nytta av UBABs stora erfarenhet och kompetens. Detta var av särskild vikt då höga hus är relativt sällsynt att man bygger i Sverige.
2. Projektering
Ett såpass komplext projekt krävde nytänkande och framför allt flexibilitet. Bland annat anpassades bjälklagsstorlekarna så varje hotellrum fick sin egen bjälklagsplatta. En slags standardisering med alla funktioner i varje platta. Vidare skapades en gjutmall runt rörgenomföringarna i schakten vilket sparade massor med tid på bygget då man slapp bygga form och gjuta runt massor av enskilda rör. UBAB utvecklade även specialgjorda magneter för att hålla spot-lampor på plats.
3. Produktion
En viktig nyckel i projektet har varit UBABs kvalitetstänkande. Peabs arbetsledare Leif Engelbrektsson: ”Produktionen på UBAB har fungerat klockrent skulle jag vilja säga. Passformen på produkterna har varit mycket bra och kvalitén på finishen mycket hög. Innertaken som skulle spacklas två gånger kan förmodligen målas direkt. Målaren är helnöjd. Det beror förstås inte bara på ytorna utan också på den smarta lösningen att varje rum är en bjälklagsplatta. Då blir det ju inga skarvar”. Han fortsätter: ”UBABs konstruktionsavdelning har verkligen ställt upp och det kändes tryggt att de är så duktiga. Fast de var lite väl hårda när vi skulle börja montera och jag bara hade en tolerans på tre millimeter mellan mina platsgjutna grundvåningar och prefabelementen. Då sa jag ifrån att sådana små toleranser är omöjliga!”
4. Logistik
Att bygga tidseffektivt är en stor utmaning i en stad av Göteborgs storlek. Det är mycket som kan gå fel, inte minst på grund av den tuffa trafiksituationen. En minutiös tidsplanering av transporterna skapade ett smart montageflöde och även största bjälklagren kunde levereras och monteras utan störmoment. De många mässorna i närområdet var också något av ett bekymmer, låt vara mindre prekärt. Leif Engelbrektsson berättar: ”Vi bävade lite inför mässperioderna. När vi släppte in lastbilarna brukade det ibland slinka in någon privatperson som man fick leda ut från byggarbetsplatsen”.
5. Montage
Montaget gick också helt enligt plan. När det platsgjutna arbetet var klart och prefabmontaget startade låg bygget åtta veckor efter tidplan, men god planering och effektivt arbete under prefabdelen gjorde att tidsplanen var i synk igen. UBABs montage skedde under 31 veckor, allt som allt levererades och monterades mer än 13 000 ton betongelement – lastat på 450 lastbilar.
6. Erfarenhetsmöte
Summa summarum: ett väl genomfört projekt med nöjda partners. Ulf Johansson, ansvarig platschef från Peab: ”Allting har fungerat väldigt bra. Från kompetent och tillgänglig projektledare till punktliga leveranser. Vi platsgjöt de allra understa våningarna och tappade några veckor men kom ikapp tack vare prefabdelen från UBAB. Så mer prefab i framtiden!”
Produktionen på UBAB har fungerat klockrent skulle jag vilja säga. Passformen på produkterna har varit mycket bra och kvalitén på finishen mycket hög. Innertaken som skulle spacklas två gånger kan förmodligen målas direkt.
Kontaktperson
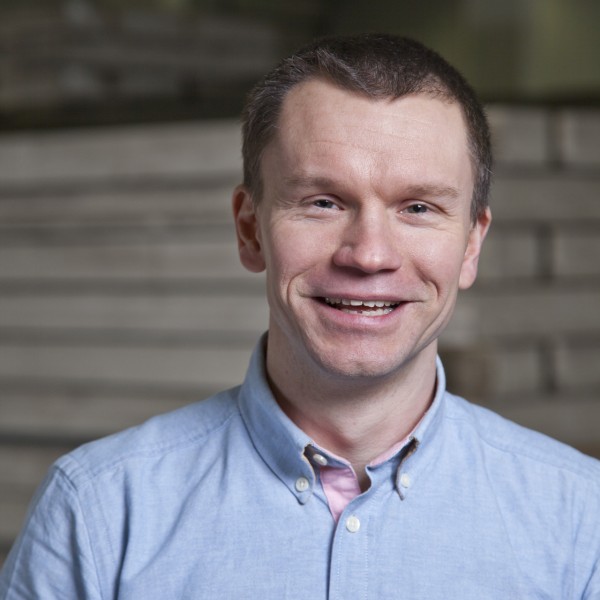
Peter Kindblom
Säljare, projektledare
peter.kindblom@ubab.com
Telefon: +46 (0)321 - 24 00 09
Mobiltelefon: +46 (0)732 - 74 85 94